Kayu lapis terbuat dari tiga atau lebih lapisan kayu tipis yang direkatkan dengan perekat. Setiap lapisan kayu, atau lapis, biasanya diorientasikan dengan serat kayu tegak lurus dengan lapisan di sebelahnya untuk mengurangi penyusutan dan meningkatkan kekuatan potongan yang sudah jadi. Sebagian besar kayu lapis ditekan menjadi lembaran datar dan besar yang digunakan dalam konstruksi bangunan. Potongan kayu lapis lainnya dapat dibentuk menjadi lengkung sederhana atau lengkung majemuk untuk digunakan dalam furnitur, perahu, dan pesawat terbang.
Penggunaan lapisan kayu tipis sebagai alat konstruksi dimulai sekitar tahun 1500 SM ketika pengrajin Mesir merekatkan potongan-potongan tipis kayu hitam gelap ke bagian luar peti mati cedar yang ditemukan di makam Raja Tut-Ankh-Amon. Teknik ini kemudian digunakan oleh orang Yunani dan Romawi untuk menghasilkan furnitur mewah dan benda-benda dekoratif lainnya. Pada tahun 1600-an, seni menghias furnitur dengan potongan-potongan kayu tipis dikenal sebagai pelapisan, dan potongan-potongan itu sendiri dikenal sebagai pelapis.
Hingga akhir tahun 1700-an, potongan-potongan veneer dipotong seluruhnya dengan tangan. Pada tahun 1797, warga Inggris Sir Samuel Bentham mengajukan paten yang mencakup beberapa mesin untuk memproduksi veneer. Dalam permohonan patennya, ia menjelaskan konsep laminasi beberapa lapisan veneer dengan lem untuk membentuk potongan yang lebih tebal—deskripsi pertama dari apa yang sekarang kita sebut kayu lapis.
Meskipun demikian, butuh waktu hampir seratus tahun lagi sebelum pelapis laminasi digunakan secara komersial di luar industri furnitur. Sekitar tahun 1890, kayu laminasi pertama kali digunakan untuk membuat pintu. Seiring dengan meningkatnya permintaan, beberapa perusahaan mulai memproduksi lembaran kayu laminasi berlapis ganda, tidak hanya untuk pintu, tetapi juga untuk digunakan pada gerbong kereta api, bus, dan pesawat terbang. Meskipun penggunaan ini meningkat, konsep penggunaan "kayu yang direkatkan", sebagaimana beberapa pengrajin menyebutnya dengan nada sarkastis, menimbulkan citra negatif terhadap produk tersebut. Untuk melawan citra ini, para produsen kayu laminasi bertemu dan akhirnya sepakat menggunakan istilah "kayu lapis" untuk menggambarkan material baru tersebut.
Pada tahun 1928, lembaran kayu lapis berukuran standar pertama yaitu 4 kaki x 8 kaki (1,2 m x 2,4 m) diperkenalkan di Amerika Serikat untuk digunakan sebagai bahan bangunan umum. Dalam beberapa dekade berikutnya, perekat yang lebih baik dan metode produksi baru memungkinkan kayu lapis digunakan untuk berbagai macam aplikasi. Saat ini, kayu lapis telah menggantikan kayu potong untuk berbagai keperluan konstruksi, dan produksi kayu lapis telah menjadi industri bernilai miliaran dolar di seluruh dunia.
Lapisan luar kayu lapis masing-masing dikenal sebagai muka dan belakang. Muka adalah permukaan yang akan digunakan atau terlihat, sedangkan bagian belakang tetap tidak digunakan atau tersembunyi. Lapisan tengah dikenal sebagai inti. Pada kayu lapis dengan lima atau lebih lapisan, lapisan tengah dikenal sebagai pita silang.
Kayu lapis dapat dibuat dari kayu keras, kayu lunak, atau gabungan keduanya. Beberapa kayu keras yang umum digunakan adalah abu, maple, mahoni, oak, dan jati. Kayu lunak yang paling umum digunakan untuk membuat kayu lapis di Amerika Serikat adalah cemara Douglas, meskipun beberapa jenis pinus, cedar, cemara, dan kayu merah juga digunakan.
Kayu lapis komposit memiliki inti yang terbuat dari papan partikel atau potongan kayu solid yang disambungkan dari ujung ke ujung. Kayu lapis ini dilapisi dengan lapisan kayu lapis pada bagian muka dan belakang. Kayu lapis komposit digunakan untuk keperluan lembaran yang sangat tebal.
Jenis perekat yang digunakan untuk merekatkan lapisan-lapisan kayu bergantung pada aplikasi khusus untuk kayu lapis yang sudah jadi. Lembaran kayu lapis kayu lunak yang dirancang untuk dipasang di bagian luar bangunan biasanya menggunakan resin fenol-formaldehida sebagai perekat karena kekuatannya yang luar biasa dan ketahanannya terhadap kelembapan. Lembaran kayu lapis kayu lunak yang dirancang untuk dipasang di bagian dalam bangunan dapat menggunakan perekat protein darah atau protein kedelai, meskipun sebagian besar lembaran interior kayu lunak sekarang dibuat dengan resin fenol-formaldehida yang sama yang digunakan untuk lembaran eksterior. Kayu lapis kayu keras yang digunakan untuk aplikasi interior dan dalam konstruksi furnitur biasanya dibuat dengan resin urea-formaldehida.
Beberapa aplikasi memerlukan lembaran kayu lapis yang memiliki lapisan tipis plastik, logam, atau kertas atau kain yang diresapi resin yang direkatkan pada bagian muka atau belakang (atau keduanya) untuk memberikan permukaan luar ketahanan tambahan terhadap kelembapan dan abrasi atau untuk meningkatkan sifat daya rekat catnya. Kayu lapis seperti itu disebut kayu lapis berlapis dan umumnya digunakan dalam industri konstruksi, transportasi, dan pertanian.
Lembaran kayu lapis lainnya mungkin dilapisi dengan pewarna cair agar permukaannya tampak akhir, atau dapat diolah dengan berbagai bahan kimia untuk meningkatkan ketahanan kayu lapis terhadap api atau ketahanan terhadap pembusukan.
Ada dua kelas besar kayu lapis, masing-masing dengan sistem pemeringkatannya sendiri.
Satu kelas dikenal sebagai konstruksi dan industri. Kayu lapis dalam kelas ini digunakan terutama untuk kekuatannya dan dinilai berdasarkan kemampuan pemaparannya dan mutu pelapis yang digunakan pada bagian muka dan belakang. Kemampuan pemaparan dapat berupa bagian dalam atau luar, tergantung pada jenis lem. Mutu pelapis dapat berupa N, A, B, C, atau D. Mutu N memiliki sangat sedikit cacat permukaan, sedangkan mutu D mungkin memiliki banyak simpul dan retakan. Misalnya, kayu lapis yang digunakan untuk sublantai di rumah dinilai "Interior CD". Ini berarti kayu lapis tersebut memiliki muka C dengan bagian belakang D, dan lemnya cocok untuk digunakan di lokasi yang terlindungi. Lapisan bagian dalam dari semua kayu lapis konstruksi dan industri terbuat dari pelapis mutu C atau D, apa pun peringkatnya.
Kelas kayu lapis lainnya dikenal sebagai kayu keras dan dekoratif. Kayu lapis dalam kelas ini digunakan terutama untuk tampilannya dan digolongkan dalam urutan menurun berdasarkan ketahanan terhadap kelembapan sebagai Teknis (Eksterior), Tipe I (Eksterior), Tipe II (Interior), dan Tipe III (Interior). Lapisan permukaannya hampir bebas dari cacat.
Ukuran
Ketebalan lembaran kayu lapis berkisar antara 0,06 inci (1,6 mm) hingga 3,0 inci (76 mm). Ketebalan yang paling umum adalah dalam kisaran 0,25 inci (6,4 mm) hingga 0,75 inci (19,0 mm). Meskipun inti, pita silang, dan bagian muka dan belakang lembaran kayu lapis dapat dibuat dari lapisan dengan ketebalan yang berbeda, ketebalan masing-masing harus seimbang di sekitar bagian tengah. Misalnya, bagian muka dan belakang harus memiliki ketebalan yang sama. Demikian pula, pita silang atas dan bawah harus sama.
Ukuran yang paling umum untuk lembaran kayu lapis yang digunakan dalam konstruksi bangunan adalah lebar 4 kaki (1,2 m) dan panjang 8 kaki (2,4 m). Lebar umum lainnya adalah 3 kaki (0,9 m) dan 5 kaki (1,5 m). Panjangnya bervariasi dari 8 kaki (2,4 m) hingga 12 kaki (3,6 m) dengan kelipatan 1 kaki (0,3 m). Aplikasi khusus seperti pembuatan perahu mungkin memerlukan lembaran yang lebih besar.
Pohon yang digunakan untuk membuat tripleks umumnya berdiameter lebih kecil daripada pohon yang digunakan untuk membuat kayu. Dalam kebanyakan kasus, pohon-pohon tersebut ditanam dan tumbuh di area milik perusahaan tripleks. Area-area ini dikelola dengan hati-hati untuk memaksimalkan pertumbuhan pohon dan meminimalkan kerusakan akibat serangga atau kebakaran.
Berikut ini adalah urutan operasi umum untuk memproses pohon menjadi lembaran kayu lapis standar berukuran 4 kaki kali 8 kaki (1,2 m kali 2,4 m):
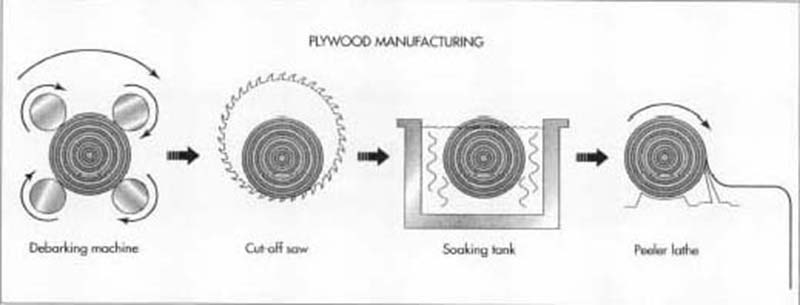
Kayu gelondongan pertama-tama dikupas kulitnya lalu dipotong menjadi balok pengupas. Untuk memotong balok menjadi potongan-potongan veneer, balok-balok tersebut direndam terlebih dahulu lalu dikupas menjadi potongan-potongan.
1 Pohon-pohon terpilih di suatu area ditandai sebagai pohon yang siap ditebang. Penebangan dapat dilakukan dengan gergaji mesin bertenaga bensin atau dengan gunting hidrolik besar yang dipasang di bagian depan kendaraan beroda yang disebut feller. Dahan-dahan pohon yang tumbang disingkirkan dengan gergaji mesin.
2 Batang pohon yang telah dipangkas, atau batang kayu, diseret ke area pemuatan dengan kendaraan beroda yang disebut skidder. Batang kayu dipotong sesuai panjang dan dimuat ke truk untuk dibawa ke pabrik kayu lapis, di mana batang kayu ditumpuk dalam tumpukan panjang yang dikenal sebagai geladak kayu.
3 Saat kayu gelondongan dibutuhkan, kayu gelondongan tersebut diangkut dari dek kayu gelondongan oleh pemuat berban karet dan diletakkan pada konveyor rantai yang membawanya ke mesin pengupas kulit kayu. Mesin ini membuang kulit kayu, baik dengan roda gerinda bergigi tajam atau dengan semburan air bertekanan tinggi, sementara kayu gelondongan diputar perlahan pada porosnya yang panjang.
4 Kayu gelondongan yang sudah dikupas kulitnya dibawa ke pabrik dengan konveyor rantai tempat gergaji bundar besar memotongnya menjadi beberapa bagian dengan panjang sekitar 8 kaki-4 inci (2,5 m) hingga 8 kaki-6 inci (2,6 m), yang cocok untuk membuat lembaran standar sepanjang 8 kaki (2,4 m). Potongan kayu gelondongan ini dikenal sebagai blok pengupas.
5 Sebelum veneer dapat dipotong, blok pengupas harus dipanaskan dan direndam untuk melunakkan kayu. Blok dapat dikukus atau direndam dalam air panas. Proses ini memakan waktu 12-40 jam tergantung pada jenis kayu, diameter blok, dan faktor lainnya.
6 Blok pengupas yang dipanaskan kemudian diangkut ke mesin bubut pengupas, di mana blok tersebut secara otomatis disejajarkan dan dimasukkan ke dalam mesin bubut satu per satu. Saat mesin bubut memutar blok dengan cepat pada porosnya yang panjang, bilah pisau berukuran penuh mengupas lembaran veneer yang terus menerus dari permukaan blok yang berputar dengan kecepatan 300-800 kaki/menit (90-240 m/menit). Saat diameter blok dikurangi menjadi sekitar 3-4 inci (230-305 mm), potongan kayu yang tersisa, yang dikenal sebagai inti pengupas, dikeluarkan dari mesin bubut dan blok pengupas baru dimasukkan ke tempatnya.
7 Lembaran veneer panjang yang muncul dari mesin bubut pengupas dapat segera diproses, atau dapat disimpan dalam baki panjang bertingkat atau digulung menjadi gulungan. Dalam hal apa pun, proses selanjutnya melibatkan pemotongan veneer menjadi lebar yang dapat digunakan, biasanya sekitar 4 kaki-6 inci (1,4 m), untuk membuat lembaran kayu lapis lebar standar 4 kaki (1,2 m). Pada saat yang sama, pemindai optik mencari bagian dengan cacat yang tidak dapat diterima, dan bagian ini dipotong, menyisakan potongan veneer dengan lebar yang lebih kecil dari lebar standar.
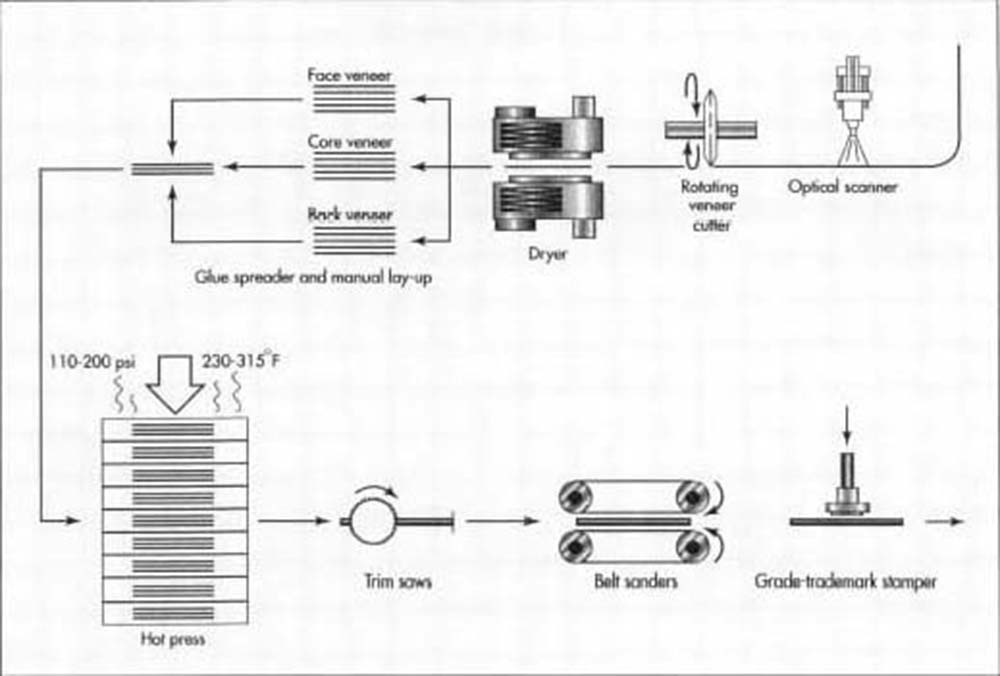
Potongan-potongan veneer basah digulung menjadi gulungan, sementara pemindai optik mendeteksi cacat yang tidak dapat diterima pada kayu. Setelah kering, veneer diurutkan dan ditumpuk. Bagian-bagian veneer yang dipilih direkatkan. Pengepres panas digunakan untuk menyegel veneer menjadi satu bagian kayu lapis yang kokoh, yang akan dipangkas dan diampelas sebelum dicap dengan mutu yang sesuai.
8 Bagian-bagian veneer kemudian disortir dan ditumpuk menurut mutu. Hal ini dapat dilakukan secara manual, atau dapat dilakukan secara otomatis menggunakan pemindai optik.
9 Bagian-bagian yang telah disortir dimasukkan ke dalam pengering untuk mengurangi kadar airnya dan membiarkannya menyusut sebelum direkatkan. Sebagian besar pabrik kayu lapis menggunakan pengering mekanis yang menggerakkan potongan-potongan tersebut secara terus-menerus melalui ruang yang dipanaskan. Pada beberapa pengering, semburan udara panas berkecepatan tinggi ditiupkan ke seluruh permukaan potongan-potongan tersebut untuk mempercepat proses pengeringan.
10 Saat bagian-bagian veneer keluar dari pengering, bagian-bagian tersebut ditumpuk menurut mutu. Bagian-bagian yang kurang lebar memiliki veneer tambahan yang disambung dengan selotip atau lem untuk membuat bagian-bagian yang sesuai untuk digunakan di lapisan dalam di mana penampilan dan kekuatan kurang penting.
11 Bagian-bagian veneer yang akan dipasang melintang—bagian inti dalam lembaran tiga lapis, atau pita melintang dalam lembaran lima lapis—dipotong menjadi panjang sekitar 4 kaki-3 inci (1,3 m).
12 Ketika bagian-bagian veneer yang sesuai dirakit untuk produksi kayu lapis tertentu, proses penataan dan perekatan potongan-potongan tersebut dimulai. Proses ini dapat dilakukan secara manual atau semi-otomatis dengan mesin. Dalam kasus lembaran tiga lapis yang paling sederhana, veneer bagian belakang diletakkan rata dan dijalankan melalui penyebar lem, yang mengoleskan lapisan lem ke permukaan atas. Bagian-bagian pendek dari veneer inti kemudian diletakkan melintang di atas bagian belakang yang direkatkan, dan seluruh lembaran dijalankan melalui penyebar lem untuk kedua kalinya. Akhirnya, veneer bagian depan diletakkan di atas inti yang direkatkan, dan lembaran tersebut ditumpuk dengan lembaran-lembaran lain yang menunggu untuk dimasukkan ke dalam mesin cetak.
13 Lembaran yang direkatkan dimasukkan ke dalam mesin pres panas dengan beberapa bukaan. Mesin pres dapat menangani 20-40 lembar sekaligus, dengan setiap lembar dimasukkan ke slot terpisah. Setelah semua lembar dimuat, mesin pres akan menekannya bersama-sama di bawah tekanan sekitar 110-200 psi (7,6-13,8 bar), sementara pada saat yang sama memanaskannya hingga suhu sekitar 230-315° F (109,9-157,2° C). Tekanan tersebut memastikan kontak yang baik antara lapisan-lapisan veneer, dan panas menyebabkan lem mengering dengan baik untuk kekuatan maksimum. Setelah jangka waktu 2-7 menit, mesin pres dibuka dan lembaran-lembaran tersebut diturunkan.
14 Lembaran kasar kemudian melewati serangkaian gergaji, yang memangkasnya hingga mencapai lebar dan panjang akhir. Lembaran dengan mutu yang lebih tinggi melewati serangkaian pengamplas sabuk selebar 4 kaki (1,2 m), yang mengampelas bagian muka dan belakang. Lembaran dengan mutu menengah diampelas secara manual untuk membersihkan area yang kasar. Beberapa lembar dijalankan melalui serangkaian mata gergaji bundar, yang memotong alur dangkal di bagian muka untuk memberikan tampilan bertekstur pada kayu lapis. Setelah pemeriksaan akhir, cacat yang tersisa diperbaiki.
15 Lembaran yang sudah jadi diberi cap merek dagang yang memberikan informasi kepada pembeli tentang tingkat paparan, mutu, nomor pabrik, dan faktor lainnya. Lembaran dengan merek dagang yang sama diikat bersama dalam tumpukan dan dipindahkan ke gudang untuk menunggu pengiriman.
Sama halnya dengan kayu, tidak ada yang namanya sepotong kayu lapis yang sempurna. Semua potongan kayu lapis memiliki sejumlah cacat tertentu. Jumlah dan lokasi cacat ini menentukan mutu kayu lapis. Standar untuk kayu lapis konstruksi dan industri ditetapkan oleh Standar Produk PS1 yang disiapkan oleh National Bureau of Standards dan American Plywood Association. Standar untuk kayu lapis kayu keras dan dekoratif ditetapkan oleh ANSIIHPMA HP yang disiapkan oleh American National Standards Institute dan Hardwood Plywood Manufacturers' Association. Standar ini tidak hanya menetapkan sistem pemeringkatan untuk kayu lapis, tetapi juga menentukan kriteria konstruksi, kinerja, dan aplikasi.
Meskipun kayu lapis memanfaatkan pohon secara cukup efisien—pada dasarnya memisahkan dan menyatukannya kembali dalam konfigurasi yang lebih kuat dan lebih bermanfaat—masih ada banyak limbah yang melekat dalam proses pembuatannya. Dalam kebanyakan kasus, hanya sekitar 50-75% dari volume kayu yang dapat digunakan pada pohon yang diubah menjadi kayu lapis. Untuk meningkatkan angka ini, beberapa produk baru sedang dikembangkan.
Satu produk baru disebut papan untai berorientasi, yang dibuat dengan mencabik seluruh kayu gelondongan menjadi untaian, alih-alih mengupas lapisan tipis dari kayu gelondongan dan membuang intinya. Untaian tersebut dicampur dengan perekat dan dipadatkan menjadi lapisan-lapisan dengan arah serat kayu yang satu. Lapisan-lapisan yang dipadatkan ini kemudian diorientasikan tegak lurus satu sama lain, seperti kayu lapis, dan direkatkan bersama-sama. Papan untai berorientasi sama kuatnya dengan kayu lapis dan harganya sedikit lebih murah.
Waktu posting: 10-Agu-2021